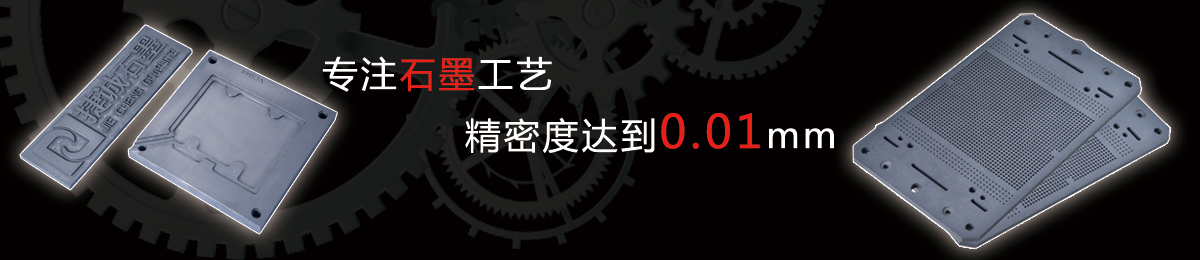
多年石墨專家告訴你什么是高純石墨
機(jī)電學(xué)院材料科學(xué)與工程教授,捷誠(chéng)石墨先進(jìn)碳材首席科學(xué)家。
2 人贊同了該文章
高純石墨指的是純度較高的石墨。石墨原材料有很多種,按照生產(chǎn)時(shí)代的成型方式,可以分為等靜壓石墨、模壓石墨、擠壓石墨,模壓石墨即是高純石墨,這種石墨是經(jīng)過(guò)10000噸的液壓機(jī)模壓而成,然后經(jīng)過(guò)幾個(gè)月的焙燒,才會(huì)形成成品。所以,高純石墨的純度較高,各項(xiàng)物理性能較好,在各行各業(yè)都有廣泛的應(yīng)用,是工業(yè)行業(yè)的優(yōu)質(zhì)材料。
我是捷誠(chéng)石墨石墨集團(tuán)的徐經(jīng)理,在石墨行業(yè)從業(yè)5年,一直鉆研高純石墨的生產(chǎn)工藝與優(yōu)化方法,研發(fā)出了比傳統(tǒng)高純石墨更加優(yōu)良的捷誠(chéng)高純石墨,各向同性,抗壓抗折性能更加 ,收到了國(guó)內(nèi)外客戶的廣泛好評(píng),也和國(guó)外三大石墨廠家:德國(guó)西格里石墨、法國(guó)羅蘭石墨、美國(guó)步高石墨建立了聯(lián)合高純石墨研發(fā)中心,致力于更加 的高純石墨制品的研發(fā),為世界各國(guó)工業(yè)屆提供更加 的石墨制品。
高純石墨是指石墨的含碳量>99.99%,廣泛用于冶金工業(yè)的高級(jí)耐火材料與涂料、軍事工業(yè)火工材料安定劑、輕工業(yè)的鉛筆芯、電氣工業(yè)的碳刷、電池工業(yè)的電極、化肥工業(yè)催化劑添加劑等。
捷誠(chéng)石墨擁有進(jìn)口高純石墨生產(chǎn)線確保原材料的穩(wěn)定供應(yīng),為您的石墨應(yīng)用提供低成本的解決方案;在捷誠(chéng)石墨,您能找到 齊全的石墨規(guī)格與等級(jí)。
捷誠(chéng)石墨模壓高純石墨的產(chǎn)品特點(diǎn):
所有的高純模壓石墨都具有滿足您需求的獨(dú)特性能。高純石墨就機(jī)械強(qiáng)度、耐摩擦性、密度、硬度、導(dǎo)電率等方面具有非常廣泛的特性,并且能通過(guò)浸漬樹(shù)脂或者金屬來(lái)進(jìn)一步的提高。
由于高純石墨顆粒度細(xì)和內(nèi)部結(jié)構(gòu)同質(zhì)性,如果不考慮尺寸原因的話他可以用來(lái)代替等靜壓石墨。
捷誠(chéng)高純石墨應(yīng)用行業(yè):
單晶爐、單晶爐、炊具、多晶爐、連續(xù)澆鑄模具、電火花、電子燒結(jié)、石英、模具和零部件等行業(yè)。
捷誠(chéng)高純石墨的優(yōu)良特性:
1.熱穩(wěn)定性:針對(duì)產(chǎn)品急熱急冷的使用條件,進(jìn)行特別設(shè)計(jì)以保證產(chǎn)品質(zhì)量的可靠性。
2.耐侵蝕性:均勻細(xì)密的基體設(shè)計(jì),延緩了產(chǎn)品的受侵蝕度。
3.耐沖擊性:產(chǎn)品所能承受的熱沖擊強(qiáng)度極高,所以任何工藝處理都可以放心進(jìn)行。
4.耐酸性:特殊材料的加入顯著改善產(chǎn)品的品質(zhì),在耐酸化指標(biāo)方面表現(xiàn)卓越,并大大地延長(zhǎng)產(chǎn)品的使用壽命。
5.高熱傳導(dǎo)性:高含量的固定碳保證了良好的熱傳導(dǎo)性,縮短溶解時(shí)間,并顯著地降低了能耗。
6.金屬污染的控制:材料成分的嚴(yán)格控制,保證了溶解時(shí)產(chǎn)品對(duì)金屬?zèng)]有污染。 7.質(zhì)量穩(wěn)定性:高壓成形法的制作技術(shù)工藝和質(zhì)量保證體系更充分地保證了質(zhì)量的穩(wěn)定性。
捷誠(chéng)石墨,致力于為世界用戶提供 優(yōu)質(zhì)高純石墨!
石墨材料加工技藝的提高才是減少石墨零件崩邊的關(guān)鍵
近年來(lái),石墨模具需求大增,特別各種石墨異形零件。對(duì)歷年捷誠(chéng)石墨公司的報(bào)廢的石墨零件原因進(jìn)行分析發(fā)現(xiàn),由于零件崩邊產(chǎn)生的廢品約占20%. 由于材料難加工,加工效率低,使零件的生產(chǎn)進(jìn)度受到嚴(yán)重影響。
產(chǎn)品特點(diǎn).jpg
石墨材料具有耐燒蝕、抗熱振等性能特點(diǎn)。但是由于其材質(zhì)特殊、切削性能差,加工質(zhì)量不易保證,特別是加工中容易產(chǎn)生崩邊缺陷,這些都成為非金屬加工的瓶頸之一。
捷誠(chéng)石墨制造公司為盡快解決石墨零件崩邊問(wèn)題,提高石墨零件生產(chǎn)效率,以某型石墨前嵌環(huán)、喉襯及其組件殼體組合等機(jī)械加工為研究對(duì)象進(jìn)行技術(shù)攻關(guān),從加工方法、刀具及其切削參數(shù)等方面探索石墨材料加工技術(shù),解決石墨零件的加工難題,對(duì)夯實(shí)非金屬加工技術(shù),順利完成科研和批生產(chǎn)任務(wù)具有重要意義。
1 石墨材料簡(jiǎn)介
石墨材料主要是各種石墨模具用石墨,是由易石墨化、強(qiáng)度高、抗燒蝕性好的石油焦骨料和析焦量高的粘結(jié)劑制成。 石墨材料的生產(chǎn)過(guò)程包括混捏、磨粉、壓制、焙燒、石墨化等工序。在生產(chǎn)過(guò)程中經(jīng)過(guò)多次熱循環(huán),材料內(nèi)部可能產(chǎn)生裂紋、氣孔等缺陷,各批材料和每塊材料內(nèi)部的性能有一定分散性。
如果實(shí)際生產(chǎn)狀態(tài)偏離工藝規(guī)程,將會(huì)導(dǎo)致石墨材料質(zhì)量波動(dòng)。比如:壓制工序是單件生產(chǎn),采用熱壓工藝。熱壓前模溫、料溫必須達(dá)到要求(135 ~ 150℃),然后將料粉裝入模具,加壓后停止模具加熱,模具自然冷卻到 50 ℃以下時(shí)允許吹風(fēng)冷卻,37 ℃以下脫模。每次壓制一件產(chǎn)品,需要五個(gè)多小時(shí),如果壓力不夠,可能產(chǎn)生氣孔、疏松、裂紋;溫度不夠,可能產(chǎn)生分層;冷卻過(guò)快,可能產(chǎn)生裂紋等。因此,石墨生產(chǎn)過(guò)程中的質(zhì)量控制對(duì)材料的性能有很大影響,如質(zhì)量控制產(chǎn)生波動(dòng),在材料上的表現(xiàn)形式是多方面的,包括裂紋、疏松、氣孔等。
石墨材料一般制成圓柱體或方形體結(jié)構(gòu),要求內(nèi)部不允許有裂紋和直徑大于1mm的空洞。
石墨材料的切削力只有切削鋁、銅等金屬材料的10%左右,車削溫度不高,最高溫度在 160~300℃之間,且與切削速度呈線性關(guān)系。但材料脆性大,加工中容易產(chǎn)生缺陷,加工表面質(zhì)量不易保證。
總之,該材料屬于難加工脆性非金屬材料,組織的致密性、均勻性與金屬相比相差甚遠(yuǎn)。
2 典型零件簡(jiǎn)介
2.1 典型零件結(jié)構(gòu)特點(diǎn)
我廠制造石墨模具零件大多為異型石墨件,結(jié)構(gòu)較為復(fù)雜。
石墨材料零部件的外觀要求:
(1)零件表面不允許有裂紋。
?。?)不允許深度超過(guò)0.1mm的劃傷,不允許深度超過(guò)0.1mm的碰傷。
?。?)不允許最大尺寸大于0.5mm的崩邊。
2.2 加工現(xiàn)狀
近年來(lái),在石墨材料加工方面做了大量的工作,成功地采用了數(shù)控加工技術(shù),使加工質(zhì)量和生產(chǎn)效率得到較大幅度的提高。但是,在加工中表面缺損、崩邊、刀具磨損嚴(yán)重等問(wèn)題尚未得到徹底解決。
微信圖片_20170907150416.jpg
3 加工難點(diǎn)分析
石墨材料具有極高的脆性,因此機(jī)械加工時(shí),容易出現(xiàn)刀具磨損嚴(yán)重、邊角崩碎等現(xiàn)象。在加工零件時(shí),機(jī)床運(yùn)動(dòng)方向的頻繁改變、刀具切入和切出時(shí)方向和角度的變化、微小的切削振動(dòng)、刀具的磨損和破 損等也會(huì)導(dǎo)致刀具對(duì)工件產(chǎn)生沖擊,造成零件崩邊、刀具磨損嚴(yán)重等許多問(wèn)題。
石墨材料的的車削過(guò)程大致是:在刀具切削刃與工件接觸時(shí),工件的一部分因刀具推進(jìn)發(fā)生破碎,形成“切屑”,切屑散落于刀具表面或堆積在前刀面,大多數(shù)切屑沿前刀面滑動(dòng),因而容易產(chǎn)生刀具月牙洼磨損。
另一方面,石墨材料的致密性、均勻性遠(yuǎn)比金屬差,切削中刀尖承受的沖擊力更大,也更容易造成刀具磨損、零件崩邊。
4 解決措施
4.1 改進(jìn)加工方法
4.1.1 優(yōu)化切削路徑
前嵌環(huán)、喉襯是由棒材加工成圓管,再由圓管加工成錐套,錐面上的余量較大。原來(lái)采用的是與錐面母線方向平行的“等距法”,加工路徑如圖7所示。這種切削方法空行程路徑長(zhǎng),加工效率低下。如果要提高效率,就得提高切削用量,刀具耐用度會(huì)降低,容易出現(xiàn)崩邊缺陷。
微信圖片_20170907150227.jpg
在保證零件質(zhì)量的前提下,進(jìn)行改進(jìn),采用“平行切法”加工錐面,粗車去余量,路徑如圖8(a);再按圖8(b)所示的路徑精車,將切削退出位置設(shè)置在錐面內(nèi)部,避開(kāi)棱邊處。這樣,不僅加工效率提高了50%以上,而且對(duì)防止崩邊缺陷起到有效地作用。
微信圖片_20170907150245.jpg
4.1.2 分粗、精加工
如上所述,前嵌環(huán)、喉襯加工余量大,材料脆、硬、均勻性差,加工中帶有沖擊現(xiàn)象。為消除切削中出現(xiàn)崩邊缺陷,同時(shí)提高加工效率,分粗、精加工是解決問(wèn)題的技術(shù)途徑之一。
將現(xiàn)場(chǎng)的加工程序優(yōu)化為粗、精加工,分別由粗、精刀具進(jìn)行加工。粗加工以提高加工效率為主,切削深度一般取0.7~1mm;精加工對(duì)粗加工后的表面進(jìn)行精細(xì)加工修復(fù),采用小切深加工,切削深度一般用0.1~0.25mm. 這樣大大提高了刀具耐用度(刃口鋒利的持久性),有效防止了因刀具磨損而損 壞導(dǎo)致的崩邊缺陷。
4.2 選擇合適的刀具與切削參數(shù)
由于石墨材料脆性較高,致密度較差,故切削刀具應(yīng)滿足硬度高、鋒利、耐沖擊與耐磨性良好等基本要求。
人造金剛石是一種超硬材料,它是在高溫、高壓和其他條件配合下由石墨轉(zhuǎn)化而成的。制成刀片形狀鑲焊在刀桿上,用于車削。人造金剛石的硬度很高,耐磨性很好,適用于加工非鐵金屬、非金屬材料。
立方氮化硼是用高溫、高壓的方法制成的,原料是結(jié)構(gòu)與石墨相似的六方氮化硼。該材料與人造金剛石相比,硬度略低,但熱穩(wěn)定性好,適用于加工黑色金屬和難加工材料。
硬質(zhì)合金硬度較高,耐磨性較好,但刃口不易磨鋒利。
因此,選用人造金剛石、立方氮化硼、硬質(zhì)合金等三種硬度較高、耐磨性較好的刀具材料進(jìn)行切削對(duì)比。
為選擇三種刀具對(duì)應(yīng)的合適切削參數(shù),先進(jìn)行了摸底切削試驗(yàn):
由于機(jī)床本身轉(zhuǎn)速限制,切削的線性速度最高可以在130m/min~150m/min之間。進(jìn)給深度按4.1.2中設(shè)置。
人造金剛石刀具,切削的線性速度設(shè)置在 150m/min,進(jìn)行切削T705石墨材料100件,發(fā)現(xiàn)刀具磨損正常,而且零件加工質(zhì)量穩(wěn)定。
立方氮化硼刀具,切削線性速度設(shè)置在120 m/min ~ 150 m/min之間,進(jìn)行切削T705石墨材料,加工60~80件零件后刀面磨損嚴(yán)重,且由于刀具磨損造成個(gè)別零件輕微崩邊;切削線性速度設(shè)置在80m/min~100m/min之間,刀具磨損正常。
選用硬質(zhì)合金刀具,切削速度在100m/min ~ 120m/min以之間,刀具急劇磨損,無(wú)法進(jìn)行正常切削:切削速度在80 m/min ~ 100 m/min 之間,加工50件石墨零件后,刀具磨損嚴(yán)重,且由于刀具磨損造成個(gè)別零件崩邊;切削線性速度在80 m/min以下,刀具磨損正常。
選用硬質(zhì)合金刀具加工時(shí),刀具前角對(duì)加工質(zhì)量也存在明顯的影響。分別采用正前角和負(fù)前角各加工10件零件。切削效果:采用正前角加工時(shí)候,切削力比較小,零件表面質(zhì)量穩(wěn)定。采用負(fù)前角加工時(shí),發(fā)現(xiàn)其中5 件零件發(fā)現(xiàn)零件存在不同程度的崩邊。
…
結(jié)論:石墨的車削效果與刀具前角γ密切相關(guān),采用正前角切削時(shí),壓應(yīng)力較小,可減少已加工表面破碎,有利于提高工件表面質(zhì)量。采用負(fù)前角切削時(shí),壓應(yīng)力增大,可促進(jìn)石墨材料的破碎,更易形成大塊的斷裂塊屑。
結(jié)論:金剛石刀具加工石墨材料效果更好,耐用度最高,為加工中首選刀具;其次選用硬質(zhì)合金刀具;不推薦使用立方氮化硼刀具。
4.3 改善排屑條件